Usines et budget 2025 : Les meilleures pratiques budgétaires pour une maîtrise totale des coûts
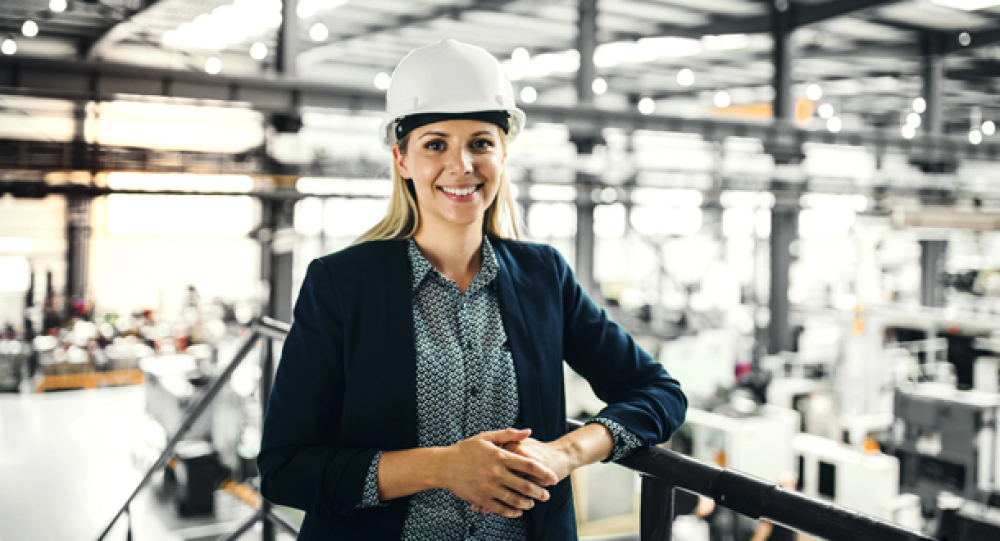
Partagez sur les réseaux sociaux
Le 30 octobre 2024
2025 marque un tournant décisif pour le secteur manufacturier. Avec des exigences budgétaires et de performance de plus en plus élevée, les directeurs d’usines sont poussés à repenser leurs stratégies pour maintenir la compétitivité tout en restant dans les limites budgétaires. Dans ce contexte, les technologies émergentes et les méthodes de gestion modernes offrent des solutions novatrices et efficaces. Cet article présente les pratiques budgétaires les plus prometteuses pour atteindre ces objectifs, avec des résultats concrets et des approches éprouvées.
Automatisation et robotisation : L’essor des cobots pour une productivité renforcée
Face à des coûts de main-d’œuvre croissants et à une pression constante sur la productivité, l’automatisation devient une solution clé pour les usines. Aujourd’hui, l’arrivée des robots collaboratifs, ou cobots, transforme l’approche de production en intégrant des machines qui travaillent aux côtés des opérateurs. Ces avancées permettent aux directeurs d’usine de réduire les erreurs humaines, d’augmenter l’efficacité et de maximiser l’utilisation de l’espace sans dépenses importantes de réaménagement.
Approches concrètes :
-
Sélection des tâches répétitives : Identifier les opérations répétitives les plus chronophages et sujettes aux erreurs humaines, où les cobots peuvent avoir un impact immédiat.
-
Phase de test et ajustements : Installer les cobots dans une zone test pour observer leur interaction avec les employés et ajuster les paramètres pour garantir une productivité optimale.
-
Formation des employés : Former les opérateurs à travailler en collaboration avec les cobots, réduisant ainsi la courbe d’apprentissage et maximisant l’efficacité.
-
Suivi et analyse des performances : Mesurer régulièrement les gains de productivité et les réductions de coûts pour ajuster les processus et étendre les cobots à d’autres secteurs de l’usine.
Selon une étude de Deloitte, les usines intégrant des cobots dans leurs chaînes de production enregistrent une réduction des coûts de main-d’œuvre de 20 à 30 % et une augmentation de la productivité de 40 % dans les deux premières années.
IA et prévision budgétaire : Prendre les devants face aux fluctuations de coût
Dans un contexte de volatilité des prix des matières premières, l’IA est devenue un outil incontournable pour renforcer la précision des prévisions budgétaires. En fournissant des analyses en temps réel et des prévisions affinées, l’IA permet aux directeurs d’usine de prendre des décisions plus éclairées et d’anticiper les variations de coût. Cela se traduit par une gestion budgétaire plus stable, évitant les surprises financières en cours d’exercice.
Approches concrètes :
-
Intégration de l’IA dans la collecte de données : Automatiser la collecte de données sur les coûts et la consommation de matières premières pour une vision exhaustive des dépenses.
-
Évaluation des scénarios de coût : Analyser différentes projections de prix avec des modèles IA pour anticiper les fluctuations et ajuster les commandes en conséquence.
-
Ajustement des prévisions en continu : Mettre à jour les prévisions de manière dynamique en fonction des données récentes et des tendances de marché.
-
Planification des achats stratégiques : Ajuster le calendrier des achats pour tirer parti des prix les plus favorables, en s’appuyant sur les prévisions de l’IA.
Selon McKinsey, les entreprises qui utilisent l’IA pour les prévisions de coûts voient une amélioration de précision de 50 % et une réduction des dépenses liées aux imprévus de 15 % à 20 %.
Efficacité énergétique et durabilité : Maîtriser les dépenses dans une perspective écoresponsable
Alors que les prix de l’énergie augmentent et que les réglementations environnementales se resserrent, les entreprises sont poussées à réduire leur consommation d’énergie. L’efficacité énergétique, combinée aux sources renouvelables, devient non seulement une priorité écologique, mais aussi une stratégie de réduction des coûts pour les directeurs d’usine.
Approches concrètes :
-
Audit énergétique complet : Effectuer un audit pour identifier les postes les plus énergivores et cibler les améliorations possibles.
-
Investissement dans des équipements à haute efficacité : Remplacer les équipements obsolètes par des versions à faible consommation énergétique, comme l’éclairage D.E.L. et les moteurs basse consommation.
-
Installation de systèmes d’énergie renouvelable : Utiliser des panneaux solaires ou des pompes à chaleur pour réduire la dépendance aux réseaux énergétiques traditionnels.
-
Suivi et optimisation : Mettre en place des capteurs pour suivre la consommation d’énergie en temps réel et ajuster l’utilisation pour réduire les pics de consommation.
L’Agence internationale de l’énergie (AIE) estime que les usines qui investissent dans l’efficacité énergétique réalisent des économies allant de 20 % à 30 % sur leurs dépenses énergétiques annuelles.
Optimisation de la logistique : Transformer la chaîne d’approvisionnement en avantage compétitif
Les coûts logistiques représentent une part importante des dépenses manufacturières. L’optimisation de la chaîne d’approvisionnement permet non seulement de réduire ces coûts, mais aussi d’améliorer la rapidité et la qualité de service. Avec l’adoption de solutions de gestion en temps réel, les directeurs d’usine peuvent désormais gérer leurs stocks et approvisionnements de façon plus agile.
Approches concrètes :
-
Centralisation des données logistiques : Centraliser les informations sur les stocks et les flux de produits pour une meilleure visibilité et prise de décision.
-
Suivi des inventaires en temps réel : Utiliser des systèmes RFID ou de code-barres pour automatiser la gestion des stocks et éviter les surcharges ou les ruptures.
-
Planification des transports optimisée : Optimiser les trajets de livraison et de réapprovisionnement pour réduire les coûts de transport et les délais.
-
Partenariats avec des fournisseurs fiables : Travailler avec des partenaires logistiques pour garantir la ponctualité et la qualité de l’approvisionnement.
Une étude de PwC indique que les entreprises manufacturières optimisant leur logistique réalisent en moyenne une réduction de 15 % à 20 % des coûts d’inventaire et de stockage.
Culture de l’amélioration continue et formation : Investir dans les compétences pour réduire les pertes
Dans un environnement où chaque minute d’arrêt représente des pertes importantes, l’amélioration continue et la formation deviennent des atouts stratégiques. En intégrant les pratiques du lean management et en offrant des formations régulières, les directeurs d’usine favorisent la productivité et réduisent les erreurs. Cette approche encourage également l’engagement des employés, qui se sentent plus investis dans la réussite de l’entreprise.
Approches concrètes :
-
Audit des processus : Effectuer un audit de chaque étape de production pour identifier les sources de gaspillage et les optimiser.
-
Mise en œuvre des méthodes lean et Six Sigma : Adopter ces méthodologies pour améliorer la qualité des processus et réduire les pertes.
-
Formation continue du personnel : Mettre en place des programmes réguliers pour enseigner les meilleures pratiques et les nouvelles technologies.
-
Suivi des résultats et réajustements : Évaluer les gains obtenus et ajuster les formations pour cibler les points faibles identifiés.
Le Lean Enterprise Institute rapporte que les entreprises ayant adopté le lean management et la formation continue constatent une réduction des gaspillages de 30 % à 35 %.
Des KPI évolués et en temps réel : Une nouvelle ère de suivi de la performance et de réactivité
Dans un monde industriel où chaque décision peut impacter directement la rentabilité, les indicateurs de performance traditionnels montrent leurs limites. Trop souvent, les KPI de base peuvent être contournés ou manipulés par les plus avisés, ce qui fausse les résultats et freine l’efficacité budgétaire. C'est ici que les KPI de nouvelle génération redéfinissent les règles du jeu. Grâce aux technologies d’IA et aux outils d’analyse en temps réel, ces indicateurs deviennent des baromètres fiables, assurant un suivi précis et quasi instantané des performances.
Une gestion en boucle fermée et une précision inégalée : Les KPI modernes ne se contentent pas de mesurer des données statiques ; ils sont intégrés dans des systèmes intelligents capables de détecter automatiquement les anomalies et d’alerter les responsables avant que les écarts ne se transforment en problèmes budgétaires. L’IA joue ici un rôle déterminant, en analysant des schémas complexes pour anticiper les dérives et suggérer des ajustements en temps réel, rendant pratiquement impossible toute tentative de manipulation.
Des instruments incontournables pour une réactivité optimale : Ces KPI évolués permettent aux directeurs d’usine de rester en phase avec chaque aspect de la production et des coûts. En fournissant une vue d'ensemble dynamique et en temps réel, ils favorisent une réactivité immédiate face aux écarts, transformant ainsi le contrôle budgétaire en un processus actif et agile. Pour les leaders qui veulent se démarquer, adopter ces KPI avancés signifie embrasser une gestion proactive, où chaque donnée contribue à une meilleure prise de décision et à un budget parfaitement maîtrisé.
En résumé, les KPI de nouvelle génération propulsent l’industrie vers une gestion budgétaire rigoureuse et infaillible, répondant aux exigences d'un secteur en constante évolution et résistant aux aléas économiques. Ils ne sont plus seulement des outils, mais des partenaires stratégiques dans l’optimisation continue des performances industrielles.
Approches concrètes :
-
Identification et hiérarchisation des KPI stratégiques : Sélectionner des KPI critiques qui couvrent tous les aspects opérationnels clés, tels que les coûts de production, l’efficacité des équipements, la qualité des produits et les délais de livraison. Ces KPI doivent être choisis en fonction de leur impact direct sur le budget et la productivité, de manière à éviter tout contournement des objectifs.
-
Intégration de l’IA pour un suivi en temps réel et des alertes intelligentes : Mettre en place des systèmes d’IA capables d’analyser des schémas et d’identifier des anomalies dans les performances. Ces outils peuvent générer des alertes automatiques dès qu’un KPI s’écarte des normes établies, permettant ainsi une intervention immédiate des directeurs d’usine.
-
Analyse prédictive et simulation des scénarios : Utiliser des outils d’analyse prédictive pour anticiper les écarts potentiels en fonction des tendances actuelles et des données passées. En simulant différents scénarios (hausse des coûts, baisse de productivité, etc.), l’IA peut suggérer des ajustements proactifs, réduisant les risques budgétaires avant même qu’ils ne se concrétisent.
-
Tableaux de bord dynamiques et personnalisés : Déployer des tableaux de bord interactifs qui offrent aux directeurs une vue en temps réel et personnalisée de chaque KPI. Ces tableaux permettent d’identifier rapidement les écarts et de visualiser les impacts budgétaires potentiels. En se concentrant sur les indicateurs les plus critiques, les dirigeants peuvent ajuster leurs priorités en fonction des évolutions en temps réel.
-
Réévaluation continue et ajustement des KPI : En fonction des résultats obtenus, réviser périodiquement les KPI pour s’assurer qu’ils demeurent alignés avec les objectifs stratégiques de l’usine. Cette approche itérative permet de maintenir la pertinence des indicateurs et d’éviter toute stagnation dans les pratiques de gestion de la performance.
Selon Gartner, les usines intégrant des KPI assistés par l’IA dans un cadre de gestion en temps réel ont observé une réduction de 25 % des dépassements budgétaires et une amélioration de la réactivité aux écarts de 30 %, permettant une gestion budgétaire plus précise et résiliente.
Embrasser l’innovation pour une gestion budgétaire optimale en 2025
En 2025, les directeurs d’usine ont l’opportunité unique de transformer leurs opérations et d’embrasser des pratiques qui ne se contentent pas de gérer le budget, mais qui redéfinissent la compétitivité et la durabilité de leur industrie. L’automatisation, l’intelligence artificielle, l’efficacité énergétique et les KPI en temps réel ne sont pas simplement des outils techniques ; ils incarnent une nouvelle manière de diriger, basée sur l’anticipation, la précision et l’innovation.
Les résistances au changement sont naturelles, mais chaque technologie intégrée et chaque amélioration de processus sont des pas vers une usine plus forte, plus agile et plus prête à répondre aux défis. Aujourd’hui, investir dans ces pratiques, c’est garantir un avenir stable et performant, où chaque décision repose sur des données fiables et chaque amélioration renforce la compétitivité de l’entreprise.
Les dirigeants qui adoptent cette vision ne sont pas seulement des gestionnaires de budget ; ils sont les architectes d’une industrie manufacturière résiliente et prospère. En capitalisant sur ces stratégies, vous ne faites pas qu’optimiser des coûts : vous bâtissez les fondations d’une croissance durable, assurant à votre usine un leadership inébranlable dans les années à venir.
Références
- Deloitte (2024). Industry Report on Automation and Cost Optimization. Deloitte Insights. Consulté en ligne sur https://www2.deloitte.com.
- McKinsey & Company (2024). AI-Driven Budget Forecasting in Manufacturing. McKinsey Insights. Consulté en ligne sur https://www.mckinsey.com.
- Agence internationale de l’énergie (AIE) (2023). Energy Efficiency in Industrial Sectors. International Energy Agency. Consulté en ligne sur https://www.iea.org.
- PwC (2024). Optimizing Logistics Costs: An Industry Perspective. PricewaterhouseCoopers Research. Consulté en ligne sur https://www.pwc.com.
- Lean Enterprise Institute (2024). Lean and Six Sigma: Reducing Waste in Manufacturing. Lean Enterprise Institute Publications. Consulté en ligne sur https://www.lean.org.
- Gartner (2024). Real-Time KPIs and AI-Driven Analytics for Budget Control. Gartner Research Reports. Consulté en ligne sur https://www.gartner.com.
Tendances manufacturières!